Exploring Die Cut Applications for EV Batteries
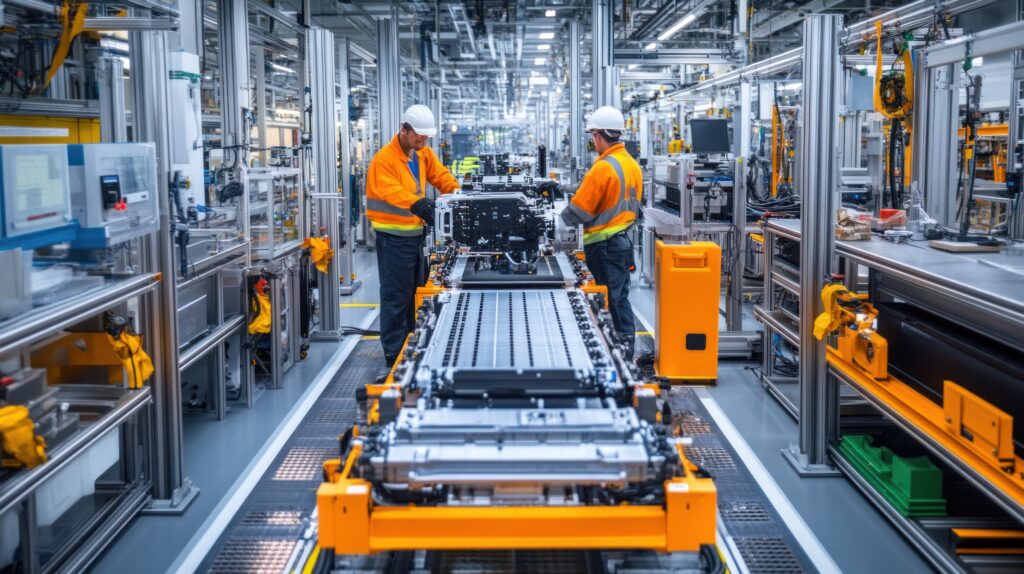
The rapid evolution of electric vehicles (EVs) has brought innovations in energy storage and manufacturing processes, particularly in the use of die-cut components for EV batteries. Die cutting, a precision manufacturing process, is integral in enhancing the performance, efficiency, and safety of modern EV batteries. This blog explores the diverse applications of die-cut components in EV battery systems.
1. Thermal Management Solutions
Effective thermal management is crucial to maintaining battery performance and safety. Die-cut thermal pads, graphite sheets, and insulating films play a significant role in heat dissipation. These components ensure that the battery operates within optimal temperature ranges, preventing overheating and improving energy efficiency.
Key Advantages:
- Improved heat distribution across battery cells.
- Enhanced lifespan of battery systems.
- Reduced risk of thermal runaway events.
2. Electrical Insulation and Shielding
Electrical insulation is paramount to ensure the safety and reliability of EV batteries. Die-cut insulating films, tapes, and gaskets help prevent short circuits and minimize electromagnetic interference (EMI). These components are designed to fit precisely within the compact architecture of EV batteries.
Applications Include:
- Insulating layers between battery cells.
- Shielding for electronic control modules.
- Gaskets to seal and protect battery enclosures.
3. Sealing and Gasketing
To protect EV batteries from environmental factors such as moisture, dust, and vibration, sealing and gasketing are essential. Die-cut seals made from silicone, foam, or rubber materials provide durable protection, ensuring the battery remains operational in extreme conditions.
Benefits:
- Enhanced durability against environmental stress.
- Improved battery enclosure integrity.
- Reduced vibration impact on battery cells.
4. Adhesive and Bonding Solutions
Die-cut adhesives and tapes streamline the assembly of battery modules by securely bonding components. These solutions offer high strength and lightweight alternatives to traditional fasteners, contributing to overall weight reduction in EVs.
Examples:
- Adhesive films for cell-to-cell bonding.
- Mounting tapes for electronic components.
- Structural adhesives for battery packs.
5. Protective Films and Laminates
Die-cut protective films safeguard sensitive battery components during manufacturing, transportation, and operation. Laminates provide additional protection against abrasion, chemical exposure, and mechanical stress.
Key Applications:
- Scratch-resistant coatings for battery surfaces.
- Protective covers for battery terminals.
- Laminates for outer casings of battery modules.
6. Noise, Vibration, and Harshness (NVH) Reduction
Die-cut foams and acoustic materials are used to minimize noise and vibration in EV battery systems. These components ensure a quieter driving experience and protect the structural integrity of the battery.
Features:
- Customizable to specific battery designs.
- Effective in damping vibrations from road conditions.
- Long-lasting performance in diverse environments.
7. Custom Die-Cut Solutions for Emerging Needs
As EV technology advances, custom die-cut solutions are being developed to address unique requirements, such as lightweight materials, recyclable components, and advanced safety features. Precision die-cutting enables manufacturers to innovate and adapt to these evolving needs.
Conclusion
Die-cut applications are indispensable in optimizing the performance, safety, and durability of EV batteries. From thermal management and electrical insulation to sealing, adhesion, and NVH reduction, die-cut components provide tailored solutions that meet the demanding requirements of modern EV battery systems. As electric vehicle technology continues to advance, the role of precision die-cutting in the battery manufacturing process will only become more critical, driving innovation and sustainability in the automotive industry.
Are you looking to integrate advanced die-cut solutions into your EV battery designs? Contact us to learn how precision die-cutting can revolutionize your manufacturing processes.