What are My Die Cut Tolerances
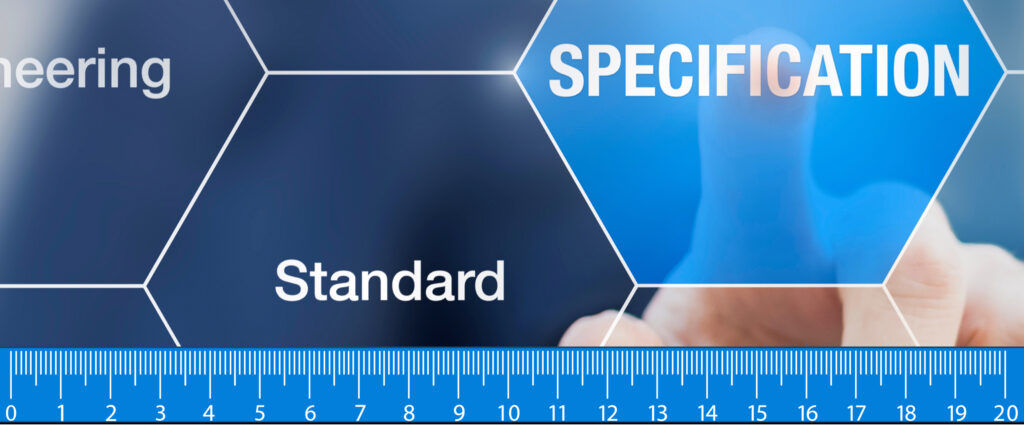
Die cut tolerances refer to the acceptable deviation from perfect precision when creating intricate and detailed designs through die cutting. Die cut tolerances are used to determine whether a die cut part has been created with adequate measurements compared to the design. With this method, different materials such as tapes, foams, foils, or even metal can be transformed into complex shapes with ease and accuracy.
It is essential to understand the limitations of these processes. Die cut tolerances are affected by factors like the thickness of material being used, the intricacy of the design being cut out, and even environmental conditions during production. Achieving tight tolerances depends on various variables such as blade sharpness, pressure applied during cutting, and quality control measures implemented throughout production.
When you submit a drawing of a part for die cutting, it’s crucial that engineers clearly define the products tolerances for both your sake and your converter’s. While some projects may require a high degree of precision with minimal tolerance for error in order to maintain integrity and aesthetic appeal; others might allow for slightly looser tolerances without compromising functionality or visual impact. Adherence to appropriate die cut tolerances ensures that final products meet desired specifications consistently while accounting for potential variations inherent in the process itself.
Tighter tolerance parts often require more expensive tools and a strict quality control process, so designs with tight tolerances cost significantly more than the alternative. In addition to design tolerances, other measurements to include in your die cut drawing are the general product dimensions and frequency of quality measurement. This will ensure that your project is specific to your needs and your project specs..
Using die cut parts and the die cutting process needs to be thought out and well designed by a converting specialist for it to be a cost effective solution for your business. Essentially, if you are looking for a series of custom, identical components, die cutting promise to improve production and final product quality. Consistent parts lead to better applications and fewer mistakes, saving time and money, while assisting with the ease of someday automating your production or scaling up your business.
Although rolls of tape cost less than die cut adhesives, they can take longer to apply, require more labor, and create a larger amount of material waste. Rolls of tape also lack the accuracy of die cut adhesives. Operators are also left on their own to figure out the best method of application, which can cause inconsistencies and errors.
Not to mention the need to hire additional staff for these task. Even with the budget to hire more people, die cutting machines can produce adhesives faster and more accurately than any employee with a pair of scissors. Often, it requires more direct contact with the final product, which can lead to issues in almost every industry.
Using a die cut solution will allow you to consolidate multi-process projects and avoid unnecessary shipping costs. Adapting designs to a die cut press increases production speed and part accuracy.