How to Improve Water-Resistance in Electronics Applications
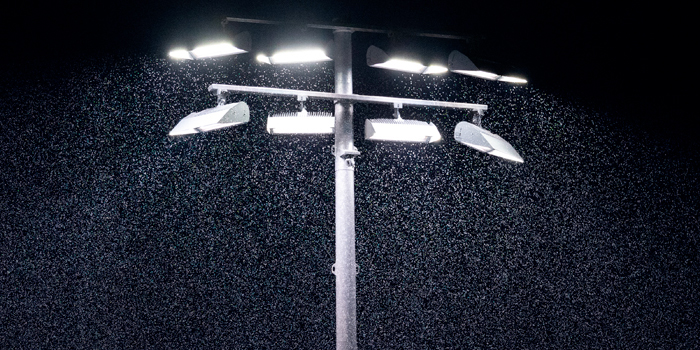
Ingress protection is extremely important in electronic device manufacturing, particularly when it comes to moisture. If housing materials aren’t bonded properly, water and other types of moisture can quickly damage electrical components and render devices inoperable. To achieve desired water resistance (or make devices truly waterproof) and provide the best possible user experience, manufacturers need to consider design and materials for ingress protection early in the product development process. Let’s look at the various levels of water resistance and how different materials and converting techniques can help improve water resistance in electronic applications.
For more tips and insights into flexible material solutions for electronic applications, download our eBook: Improving protection and performance in electronic devices. https://www.saunderscorp.com/document/improving-protection-performance-in-electronic-devices/
Water-resistant vs. waterproof
There’s a big difference between a device being water resistant and fully waterproof. Water resistance is measured according to International Protection Marking Standards and given an IP rating ranging from 0 to 9. A device with an IPX0 rating would offer no protection while an IPX9 rating would indicate protection against a high-pressure jet of directed water from any angle, including steam cleaning. Many consumer electronics products have an IP rating of around 4 or 5, offering some protection under normal conditions, but likely not protected against long exposure underwater. But it’s important for manufacturers to consider all the possible real-world use cases for the final product and make design and material decisions based on the intended application.
For example, wearable electronic devices like fitness trackers may require higher IP ratings to allow users to wear their devices while swimming for an extended period. However, for medical devices like glucose monitors, water depth may not be as important as ensuring proper adhesion to skin for prolonged periods of time without losing bond strength or damaging the user’s skin. The key is to select the optimal materials for the given application and find efficiencies in the manufacturing process to attain business objectives.
Adhesive materials
When it comes to water resistance for electronic applications, adhesive bonding materials often play a major role in sealing housing pieces and other components. 3M™ VHB tapes, for example, are commonly used because they are high-bond tapes that create a strong seal between parts and have closed cell constructions that help prevent water from leaking through. Certain foams, like 3M’s ISOLOSS™ LS Polyurethane Foam, can be used in conjunction with adhesives to form a water-tight seal under high compression.
Liquid adhesives can also be useful for bonding parts with uneven surfaces or for materials that present adhesion challenges. But liquid materials are generally harder to work with, potentially decreasing efficiency in the manufacturing process. Where possible, manufacturers should consider flexible materials like tapes, foams and foils that can offer quality ingress protection and greater manufacturability.
Gasketing
Gasketing is a tried-and-true method for improving ingress protection in electronic applications, creating a seal between components that keeps moisture out. EPDM, Neoprene, and silicone are some of the top rubber varieties used to make custom gaskets because of their water-resistant properties.
However, material selection should be about more than just ingress protection.
As electronic devices get smaller and space becomes more of a premium, gasketing materials can pull double duty and also provide thermal management and EMI shielding for greater overall protection and device performance. The key is to find a converting partner who has the expertise to guide materials selection and then achieve tight tolerances in the manufacturing process to meet exact specifications, even for small parts or materials that are generally considered difficult to tool.
Design for water resistance early
Often, design engineers wait until the later stages of the product development process to consider water resistance requirements. This can lead to rework, materials changes and additional testing that can increase costs and delay project delivery. Instead, manufacturers should consider working with a converting partner early in the process who can guide both materials selection and device design to ensure proper moisture management. This will help streamline product development overall and ensure the optimal level of water resistance is achieved for unique electronics applications.
Ready to start your next electronic device manufacturing project? Contact us today and we’ll review your requirements and explore all the ways we can add value to your operation.